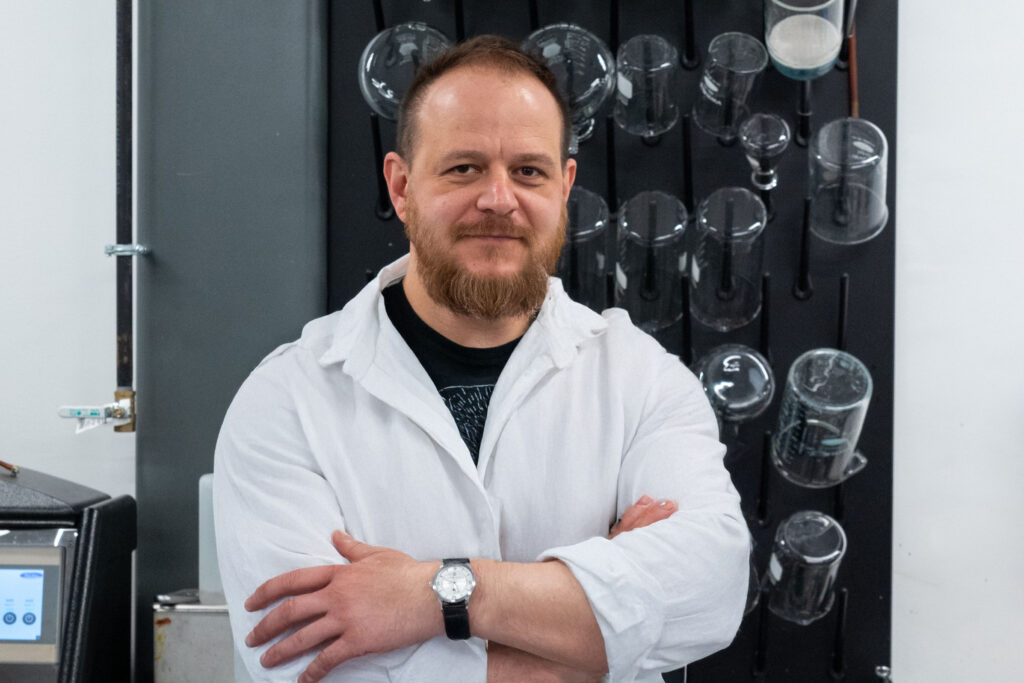
Alex, how long have you been with Sawgrass?
I have been with Sawgrass for 8 years. I started as a Product Development chemist and currently I am a director of Research and Development and Quality Control.
What are your main responsibilities here?
- Every day Quality Control of manufactured inks. We make all inks here in Charleston, SC and we have a Quality Control lab where we check the quality of manufactured inks
- Resolving customers issues. We do have a customer support teams at Sawgrass but some issues need further testing in our R&D lab
- Working on new formulations and changing/testing some of our existing formulations
- Working on future printer developments
Can you describe a typical day for you here at Sawgrass?
Every day is different here and that’s what makes it interesting. Some days we must concentrate on resolving customers’ issues and some days we have time to work on research and development of future products.
We all think of you as the guy behind our inks. What makes Sawgrass Ink so special?
All our inks are manufactured and packaged here in Charleston, South Carolina. Then we ship our cartridges around the world. Most of our competitors buy inks from other countries and then just fill the cartridges with those inks. At Sawgrass we want to control the quality of our inks at every step starting from raw chemicals.
Also, our inks are water based and do not contain any harsh solvents.
What stands out to you about our ink manufacturing process?
When we make the new ink batch, we want to make sure that this ink has the same properties and color as the ink we made 3 years ago. We test the properties and colors of every new ink batch and compare it to our original ink batch. If everything matches, we release the ink to production where they fill the cartridges. If it does not pass QC we work on adjusting properties of the ink batch until it passes the QC.
After the ink batch is approved, we keep 2 liters of ink from each batch for 2 years. If a customer is having issues with printing, we can go back and re-check the same batch to see if it is an ink issue or not.
Our support team always talks about the expiration dates on our inks. Why do those matter?
Most of our inks have 2 years shelf life. After 2 years there could be ink particle agglomerations which can damage the printhead. This is why we recommend using all the inks before the expiration date
One of the unique features of sublimation ink is its viscosity. Can you explain what that means and how it prevents clogs?
Viscosity is basically a measure of fluids resistance to flow. For example, water flows freely and the viscosity of it is very low. Honey takes much more time to flow because it is very viscous. Our inks are more viscous than water but less viscous than honey. When we formulate the inks, we need to adjust the viscosity to a certain level specific to each printhead. If you try to use inks which were not made for the printer they can have lower or high viscosity than needed and this can cause clogs and missing nozzles
I’ve been asked them many times; do you need to replace the ink before the cartridge is empty?
You do not need to replace the cartridge before it is empty. When it is time to replace the cartridge printer will have a message on the screen.
It’s always warm here, but I know it’s cold in other parts of the world. Does that impact our inks?
For the best performance we recommend that printing environment temperature is from 15 to 25 Celsius and humidity is from 40 to 60%
We say that we have one of the few printers that are purpose built specifically for sublimation printing. Why is that important?
Sublimation ink is different from office printer ink. This is why it was important to develop a printer made specifically for sublimation. There are several features in our printer which we developed specifically for sublimation. One of them is auto-cleaning option where printhead cleans itself automatically. This helps to avoid nozzle clogging issues and waste of paper. We also adjusted printer firmware so that it prints better quality images with sublimation inks
One final question: what are some things you recommend to Sawgrass Printer Owners to make sure they are getting the most out of their machines?
- Do not use 3rd party cartridges. They can damage the printhead and produce prints of poor quality
- Keep the printer powered on so it can do automatic cleanings
- Do not store printers outside or in the garage
Thank you so much for your time Alex! We hope you learned some things about Sawgrass and our Ink. Tune in next month for another insightful interview with our Sawgrass Team!